UMMC's supply chain lifeblood flows from 20,000-square-foot pump
By: Gary Pettus, gpettus@umc.edu
It’s their job to be pessimists – medical emergency forecasters whose antennae, so to speak, are tuned to the Gloom and Doom Channel, with its relentless images of epidemics, deadly storms, train derailments, mass traffic accidents.
They must know that it’s a good idea to keep extra disposable medical face masks at hand: During last year’s flu season, from September through March, the University of Mississippi Medical Center purchased more than 7,100 boxes of masks, at 20 per box, or more than 142,000 masks.
“Flu season, for us, is probably the busiest time that’s non-disaster related,” said Henry Cote, assistant manager of the department responsible for this far-sightedness: Materials Management.
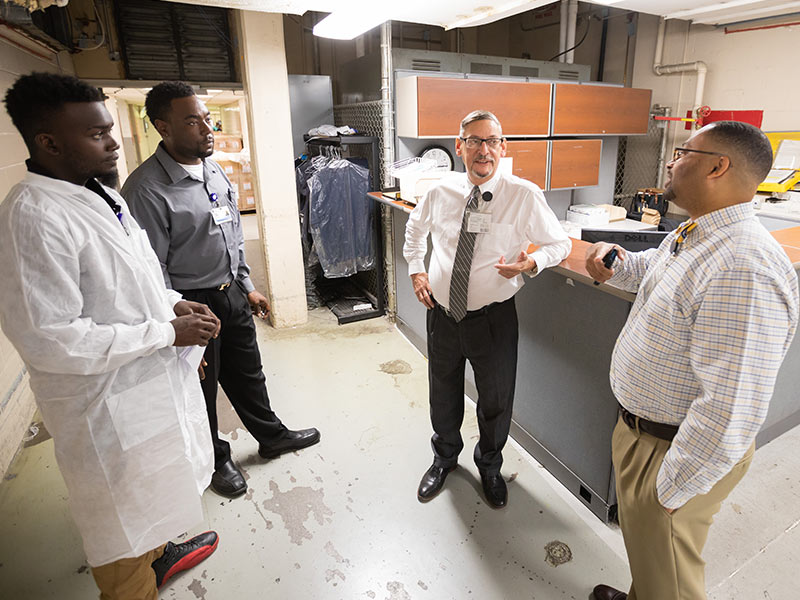
As for something disaster-related: An April 2004 passenger train derailment near Flora sent many of the 40-plus injured to UMMC, where members of the Materials Management staff made sure custom surgery packs were sent to the ER, while rushing more surgery supplies to the OR, where they were needed to treat the flood of patients.
The staff cannot know when and where outbreaks and disasters will happen, but they must assume that they will. Patients’ lives may depend on it, and those who take care of them depend on having at hand the necessities to save them, treat them, or simply make them more comfortable – deploying everything from IV fluids to Pampers.
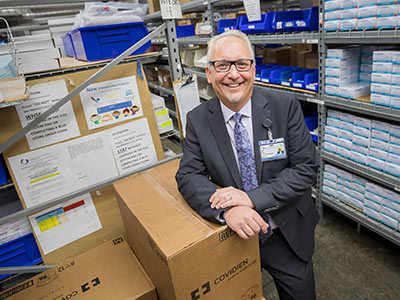
“People don’t take us for granted,” said Bill Stitt, chief of supply chain management. “They just kind of assume we’re always there.
“We’re proud of the contribution we make to patient care.”
Stitt is there with 111 full-time employees, overseeing basic commodity orders for UMMC while working with various chief executive officers and all administrators and reporting to Kevin Cook, health system CEO.
He’s in charge furnishing the varied pieces and parts of the entire Medical Center, including data management and the Post Office (leased from the U.S. Postal Service, but staffed with UMMC employees).
Cote, with his three supervisors and 19 technicians, consults mainly with nurse managers and some physicians, as well as with Stitt, to equip the campus hospitals.
“We don’t buy bags of IV fluids,” said Stitt, noting that purchases are made through state contracts. “We buy pallets. We don’t buy boxes of gloves; we buy cases.” Latex-free gloves, at that, to foil allergies.
“We give personalized service,” Cote said. That goes for patients, such as burn victims who require a wound dressing not normally in stock; and, whenever possible, for physicians who may prefer, say, a certain type of knee implant or pacemaker.
“But sometimes we don’t know what certain patients need until they get here,” Cote said.
There is a way to prepare for disasters, though: Materials Management orders relief supplies that are positioned at the Jackson-Evers International Airport for Mississippi MED-COM, which coordinates patient care and transport with emergency response agencies statewide
“Some people have trouble getting their heads around the magnitude of this place, the different supplies we order,” Cote said. The size of “this place” – that is, the warehouse – is approximately 20,000 square feet, he said.
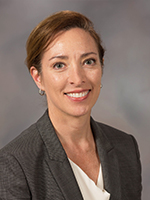
Certainly, Liz Youngblood doesn’t take for granted the scale of this effort. “Supply chain and materials management play an essential role in our ability to provide care to our patients,” said Youngblood, CEO of adult hospitals.
“Without their services we would not be able to operate the infrastructure needed for our hospitals and clinics. They touch every department and service within the health system.”
As Cote put it: “We’re like the blood running through the body.”
If so, then perhaps the heart, the pump, for that blood is the warehouse where around 1,400 products are stored in its basement location near the Post Office. That number doesn’t begin to tell the story; the department processes some 22,000 unique items, 8,000 for ORs alone, such as $10,000 stents and $6,000 catheters.
For an outsider, the network maintaining all this “blood” flow might sound as intricate as the human body.
For instance, the “vessels” connected to the warehouse “pump” extend to Richland, where Owens & Minor, a health-care services and equipment distributor, is contracted to truck in deliveries to the Jackson campus; here, starting each day at around 3:30 p.m., they’re unloaded from pallets or wheeled carts labeled and numbered to show that they are bound for specific storerooms across the Medical Center.
The workload for Materials Management demands three eight-hour shifts, with the third starting at 11 p.m.
And, although the Jackson Medical Mall, located about a 1 ½ miles from the main campus, pumps in its own deliveries – “if they don’t have what they need there, they can come here and get it,” Cote said.
Mostly, needed orders are monitored and updated automatically, through PAR Excellence Software Systems, which links UMMC’s Lawson Software to Owens & Minor. Exceptions: the Adult ER, which keeps supplies by each patient bed; Interventional Radiology; and the OR. Those orders are placed manually.
For any other non-automated areas, departments manage inventories themselves. But, no matter who handles them, it falls to Materials Management to make sure perishable items are still alive and kicking; as anyone who has ever examined the label on a bottle of aspirin or cough syrup knows, medicine isn’t forever.
So, every other Wednesday, those whose job is to keep the hospital supplied work for hours sifting through medical supplies stored in hospital bins, checking expiration dates.
They’re making sure the blood flowing through the body is sound.